Ramesh Shrestha doesn't worry about a robot replacing his job because in some ways — one already has.
Shrestha, a supervisor for commercial cleaning company Ultra Shine, has a robot named Bob as a coworker at the Westmount Centre shopping mall in Edmonton.
Bob robotically swivels around the mall's food court and stops for curious shoppers as he scrubs the floors every day. Unlike the humans who used to do this job, Bob never tires or suffers from back pain.
The robot has not replaced any of Ultra Shine's employees. The company actually has been expanding, and data from Statistics Canada shows a similar story has been playing out for years at other businesses across the country.
As for Shrestha, he considers Bob a timesaving tool that helps his team of cleaners be more productive.
"I can allocate my other colleagues to do other tasks," he said.
The robots are coming
More robots and more humans isn't an experience unique to Ultra Shine. Workplace figures from Statistics Canada show that between one and five years after robots are adopted in a workplace, firms that bring on the machines see about 20 per cent more employees than they had before adding the robots.
"On average, firms that have adopted robots have in fact expanded their workforce in aggregate," said Jay Dixon, a researcher with the federal statistics agency. Dixon's analysis looked at data collected from 1996 to 2017, tracking what happened to workers when companies in Canada invested in robots.
Some economists have also predicted the pandemic will accelerate a shift toward more automation in the workplace.
More robots could increase productivity for Canadian companies, according to Dixon. However the transition does not come without challenges, especially for the workers most likely to see their skills become obsolete.
More jobs — but fewer middle managers
Dixon's research showed that while Canadian companies tended to hire more people after investing in robots, the distribution of jobs changed, with companies hiring more lower-skilled and higher-skilled workers.
Middle-skilled workers and managers did not seem to fare as well — a phenomenon economists call job polarization.
As companies become more productive and expand, they may need more workers to supervise the new robots as well as more workers to handle tasks that are beyond the robots' abilities, such as marketing or customer service roles. But there ends up being less demand for the managers in between those roles.
Retraining those mid-career workers, who have put down roots in their communities, is a complex challenge for governments, companies and schools. Companies that adopted robots, in Dixon's study, sometimes saw the number of middle managers drop by 50 per cent over five years.
WATCH | Meet Geoffrey, a little pink robot delivering food in Toronto:
Viet Vu, a senior economist at Ryerson University's Brookfield Institute for Innovation and Entrepreneurship, said re-skilling approaches should be tied to local schools and economic development agencies.
The role of government, he said, should be investing strategically to reach companies outside established hubs such as Toronto and Vancouver.
Policies can lower incentive to innovate
Joel Blit, an economics professor at the University of Waterloo, considers the pandemic an opportunity for Canadian companies to invest in new technology and become more productive.
It is going to take the right sorts of policies … I'm not sure that Canada has the right types of policies.- Joel Blit, economist at University of Waterloo
Companies may be more motivated to automate to reduce worker interaction and prevent the spread of COVID-19, according to Blit. His research suggested other recent recessions have led to losses of more "routine" jobs in Canada, and that these jobs do not return after the recession.
But the economist told CBC Radio's The Cost of Living that more automation may not happen in this country.
- The Cost of Living ❤s money — how it makes (or breaks) us.
Catch us Sundays on CBC Radio One at 12:00 p.m. (12:30 p.m. NT).
We also repeat the following Tuesday at 11:30 a.m. in most provinces.
"It is going to take the right sorts of policies, and to be completely frank, I'm not sure that Canada has the right types of policies," he said.
The federal wage subsidy, he said, has made labour costs low, providing firms a disincentive to invest in worker-replacing robots or artificial intelligence.
He said governments should be encouraging companies to invest in new technology and putting them in touch with experts who know how to use it.
Ryerson's Viet Vu said that concern is valid, but the pandemic is an emergency unlike previous recessions.
"Given that we're still in the middle of the pandemic, the benefit of providing such income stability to both firms and workers probably outweighs the cost of delaying these kinds of technological investments," he said.
The federal government's recent budget calls artificial intelligence "one of the greatest technological transformations of our age" and proposes spending $443.9 million over ten years on a national artificial intelligence strategy.
Robots gain traction in Alberta
Regardless of how quickly changes occur, a shift toward automation is already occurring in a province not known for its robotics industry.
South of Edmonton, in Leduc, Alta., sister companies Confined Space Robotics and Spence Corrosion are using robots to improve the blasting and coating of tanks and vessels.
Sandblasting in confined spaces can be difficult and dangerous work for humans due to dust, darkness and lack of oxygen.
Foreman Tony Faulkner, who has worked for Spence Corrosion for a decade, said he was skeptical of robots replacing workers at first but realized they were more of a help than a threat.
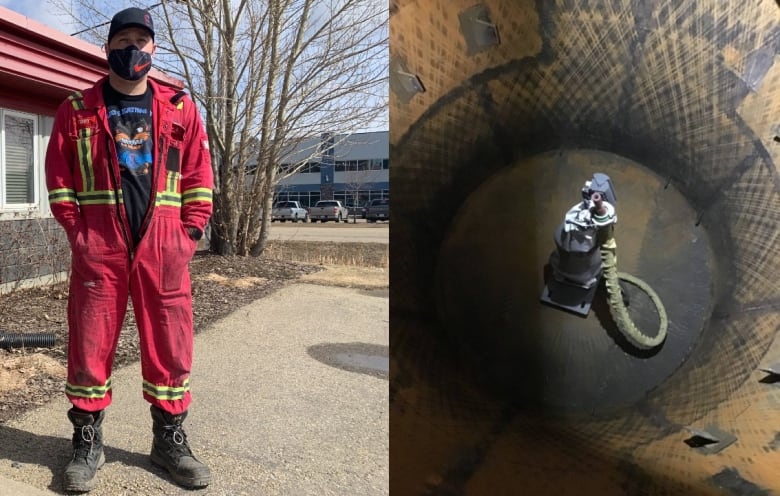
"You still need people around to be watching equipment and to be definitely watching the robot itself," he said.
Company president Norman Spence said robotics have allowed him to hire more people, but companies like his need engineers who can learn new tools and apply what they learned about robotics in school to practical problems.
"There's a really big opportunity for the province to step in and try to drive this type of both technology as well as an employee base to take care of the variety of technologies," he said.
At the Northern Alberta Institute of Technology in Edmonton, mechanical engineering technology students must now take a robotics course in order to graduate.
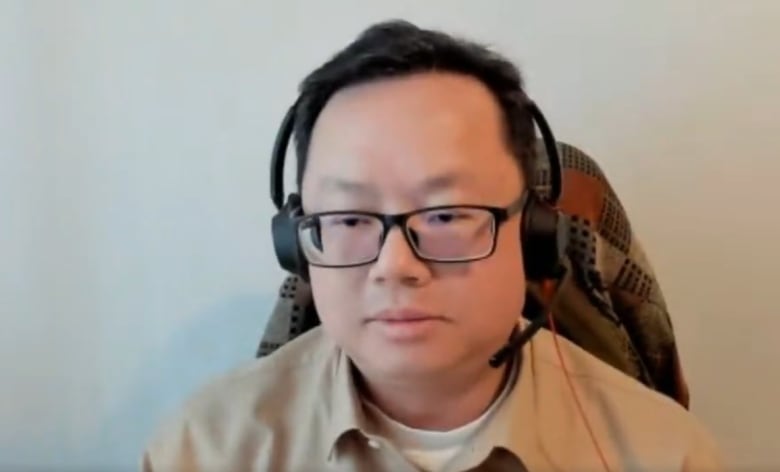
The program's academic chair, Alex Shum, said the school is responding to increased industry demand.
In recent weeks, companies have been sending him job opportunities for grads with robotics experience.
"They never asked that before," he said.
"It's almost as if everybody's looking for this right now in Alberta."
Written and produced by Madeleine Cummings.
Click the play icon above this story to hear this segment, or download the Cost of Living podcast.
The Cost of Living airs every week on CBC Radio One, Sundays at 12:00 p.m. ET (12:30 NT).
https://news.google.com/__i/rss/rd/articles/CBMi9gFodHRwczovL3d3dy5jYmMuY2EvcmFkaW8vY29zdG9mbGl2aW5nL3JvYm90cy1taWdodC10YWtlLXlvdXItam9iLWJ1dC10aGV5LWNvdWxkLWFsc28tZ2VuZXJhdGUtbmV3LW9uZXMtdGhhdC1pcy11bmxlc3MteW91LXJlLWEtbWlkZGxlLW1hbmFnZXItMS41OTk4NjY0L21vcmUtcm9ib3RzLWFyZS1lbnRlcmluZy1jYW5hZGlhbi13b3JrcGxhY2VzLWJ1dC10aGV5LXJlLW5vdC1hbGwtY29taW5nLWZvci1vdXItam9icy0xLjU5OTg4NjTSASBodHRwczovL3d3dy5jYmMuY2EvYW1wLzEuNTk5ODg2NA?oc=5
2021-04-25 08:00:00Z
CBMi9gFodHRwczovL3d3dy5jYmMuY2EvcmFkaW8vY29zdG9mbGl2aW5nL3JvYm90cy1taWdodC10YWtlLXlvdXItam9iLWJ1dC10aGV5LWNvdWxkLWFsc28tZ2VuZXJhdGUtbmV3LW9uZXMtdGhhdC1pcy11bmxlc3MteW91LXJlLWEtbWlkZGxlLW1hbmFnZXItMS41OTk4NjY0L21vcmUtcm9ib3RzLWFyZS1lbnRlcmluZy1jYW5hZGlhbi13b3JrcGxhY2VzLWJ1dC10aGV5LXJlLW5vdC1hbGwtY29taW5nLWZvci1vdXItam9icy0xLjU5OTg4NjTSASBodHRwczovL3d3dy5jYmMuY2EvYW1wLzEuNTk5ODg2NA
Tidak ada komentar:
Posting Komentar